Just How Professional Packaging Machine Repair Services Lessen Downtime and Boost Performance
Professional packaging machine repair service services are necessary in reducing downtime and enhancing efficiency through specialized diagnostics and timely treatments. The ramifications of such solutions expand past prompt repair services-- unloading the more comprehensive impact on functional performance exposes important insights into long-term efficiency approaches.
Relevance of Timely Repair Works
Prompt repair work of product packaging devices are crucial for maintaining functional effectiveness in any kind of manufacturing environment. When machinery breakdowns or breaks down, it can result in considerable interruptions in assembly line, causing raised downtime and lost earnings. The longer a product packaging equipment remains out of commission, the higher the effect on general efficiency, possibly triggering hold-ups in meeting orders and lessening consumer satisfaction.
In addition to the instant economic effects, postponed repair services can cause a lot more extensive damage to the equipment. Elements that are not resolved quickly can degrade additionally, needing more costly repair work or full substitutes, which could have been avoided via timely intervention. Routine maintenance and punctual repair services can boost the lifespan of product packaging devices, ensuring that they run at optimum efficiency degrees.
Buying specialist packaging equipment repair service solutions is essential for mitigating these threats. A proactive method to fixings not just keeps production routines yet likewise fosters a culture of dependability within the company. By prioritizing prompt fixings, organizations can maintain their affordable side, enhance source allotment, and inevitably improve their profits with enhanced operational performance.
Expertise in Diagnostics
When it comes to maintaining the efficiency of packaging devices, expertise in diagnostics plays a crucial function in identifying issues before they rise right into major failures. Experienced technicians utilize advanced analysis tools and methods to do detailed analyses of equipment efficiency. This aggressive approach enables them to determine the origin creates of breakdowns, whether they come from mechanical wear, electrical faults, or software application inconsistencies.
Effective diagnostics not only promote swift identification of problems yet additionally improve the general reliability of packaging procedures. By carrying out extensive assessments, technicians can evaluate the health of important elements, guaranteeing that also minor abnormalities are resolved immediately. This attention to information lessens the threat of unforeseen breakdowns, which can bring about expensive downtime.
In addition, expert diagnostics give useful insights right into operational patterns, enabling companies to make enlightened decisions regarding tools upgrades or alterations. By leveraging these insights, firms can enhance their product packaging processes, causing improved effectiveness and productivity. Eventually, buying analysis competence is important for companies seeking to preserve smooth operations and copyright high requirements of quality in their packaging procedures.
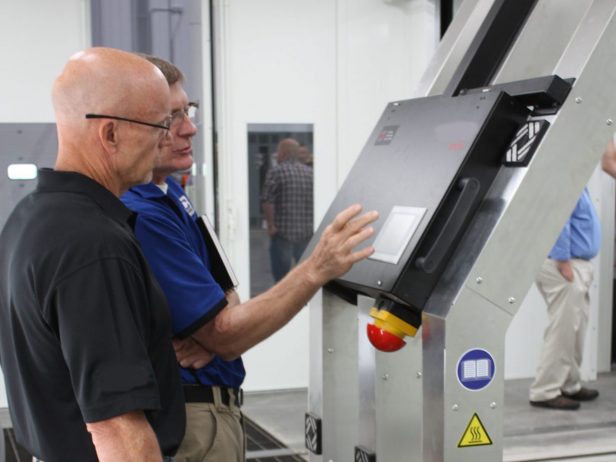
Preventive Maintenance Perks
Preventive maintenance matches expert diagnostics by proactively attending to possible issues before they materialize into severe issues. By carrying out a structured preventative upkeep program, companies can substantially lower the danger of unexpected machine failings, consequently minimizing costly downtime. Regular inspections, cleansing, and components substitute aid ensure that packaging equipment operates at ideal effectiveness.
Among the crucial advantages of preventative maintenance is its ability to extend the lifespan of equipment. By frequently preserving machinery, organizations can stay clear of the worsening results of deterioration that commonly result in significant repair services or replacements. This not only saves capital however also enhances the overall integrity of manufacturing procedures.
Furthermore, preventive maintenance adds to boosted safety and security problems within the work environment. By identifying and correcting possible dangers before they escalate, companies produce a more secure environment for their staff members (packaging machine repair service). This aggressive method not only shields employees yet also cultivates a culture of responsibility and alertness
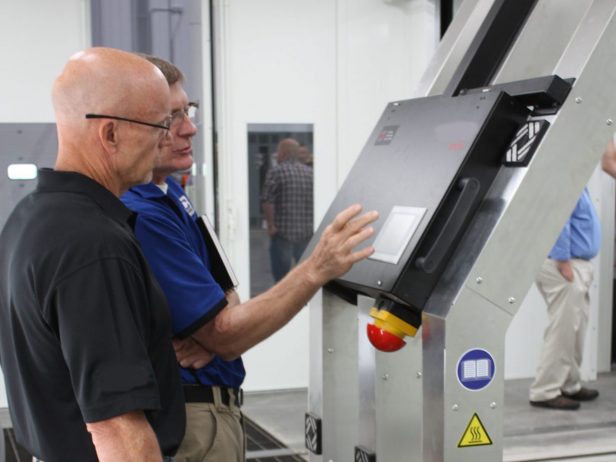
Custom-made Service Solutions
Acknowledging the one-of-a-kind needs of each service, personalized look what i found service options for product packaging machine repair work deal customized techniques that boost functional efficiency. These services are created to deal with specific obstacles faced by various sectors, ensuring that device downtime is minimized and productivity is optimized.
Specialist fixing services begin with a thorough evaluation of a business's product packaging procedures. By comprehending the details machinery entailed and the needs of the manufacturing setting, professionals can create a personalized repair and maintenance strategy. This might consist of specialized training for internal personnel, the application of predictive maintenance technologies, or the provision of dedicated support throughout optimal manufacturing times.
In addition, tailored remedies can include adaptable service agreements that align with a firm's functional timetable, permitting repairs to be performed throughout off-peak hours. By prioritizing the unique needs of each organization, these custom services ensure that fixings are not just efficient yet likewise seamlessly incorporate into existing workflows.
Inevitably, the focus on customization allows companies to maximize their packaging procedures, causing enhanced integrity and efficiency of machinery, which is crucial for keeping competitive benefit in today's hectic market.
Impact on Overall Effectiveness
Custom-made service remedies not just address particular repair service needs however likewise play a considerable role in improving general functional efficiency. By supplying targeted interventions, expert packaging device repair solutions straight decrease the regularity and period of equipment failings. This proactive technique guarantees that assembly line remain functional, decreasing disruptions that can cause costly downtime.
Moreover, reliable repair work solutions add to smoother workflows, as well-kept equipment runs at optimum performance levels. When makers operate appropriately, the quality of packaged items improves, causing less issues and less rework. This enhancement not only increases productivity however likewise reinforces consumer complete satisfaction.
Furthermore, routine maintenance and fast response times from repair professionals foster a culture of dependability within the company. Staff members can focus on their key jobs instead than fretting about possible tools failures. The general throughput of the production procedure rises, allowing firms to satisfy demand more successfully.
Inevitably, the calculated financial investment in professional repair solutions equates to boosted efficiency throughout all operational facets, guaranteeing that services can adapt and flourish in an open market. This synergy between maintenance and productivity is vital Get More Information for long-lasting success.
Conclusion
Finally, expert packaging device repair service solutions play a vital role in decreasing downtime and boosting performance within manufacturing atmospheres. Prompt repair work, professional diagnostics, and preventative maintenance add to the reliability of equipment, while personalized service options address particular functional needs. The collective effect of these solutions causes enhanced total effectiveness, allowing businesses to keep production routines, support product top quality, and successfully satisfy market demands. Purchasing such services eventually drives continual functional success (packaging machine repair service).
Comments on “Top packaging machine repair service to keep your business on track.”